The Ultimate Guide to Self-Contained Loaders for Plastics Processing

Clearing the Confusion: Loaders vs. Receivers
Before we dive into choosing the right loader, let’s clear up a common point of confusion. Many processors use the terms “loader” and “receiver” interchangeably, but they are not the same thing. Understanding this distinction upfront will help you make the right decision for your operation.
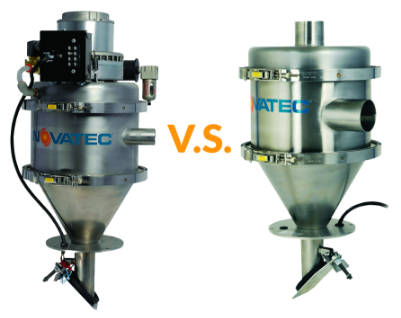
- Self-Contained Loaders have a built-in motor—no external vacuum pump needed. They pull material directly from a storage bin to a processing machine and are best for injection molding, extrusion, and localized material delivery.
- Vacuum Receivers have no motor of their own and instead rely on a central vacuum pump. These are used in central vacuum systems, where multiple machines share material from a common source, making them ideal for larger-scale processors.
If you need a standalone material loader for a few machines, a self-contained loader is the way to go. If you’re dealing with a large facility that requires centralized control, a receiver-based system may be the better long-term investment—but that’s a topic for another guide.
So if you’re looking for self-contained loaders, keep reading. If you need vacuum receivers, check out our Ultimate Guide to Vacuum Receivers.
1. Why Choosing the Right Loader is Crucial for Your Operation
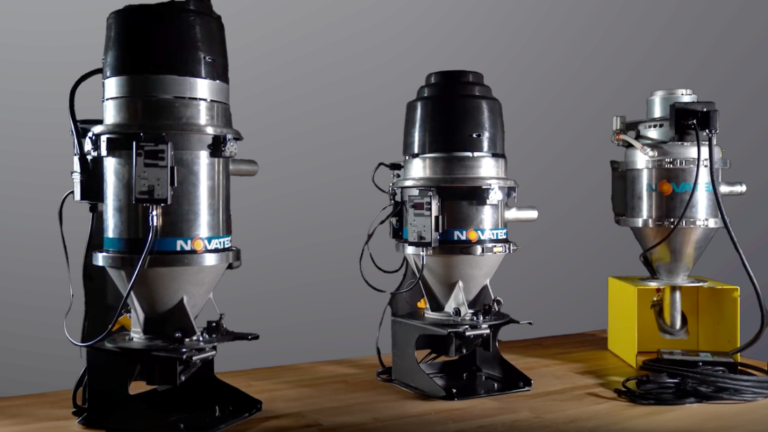
In plastics processing, few things matter more than keeping materials flowing efficiently. When resin, regrind, or powder isn’t reliably making it from storage to your machines, everything grinds to a halt—costing you time, money, and production.
That’s why vacuum loaders are a critical part of any operation. These small but mighty machines automate material handling, ensuring your equipment is fed consistently and efficiently without significant manual labor.
Yet, many processors overlook loaders until something goes wrong. And when they do, the problems start piling up:
- Starved machines – Production stalls because materials aren’t getting to where they need to be.
- Clogged filters & blockages – More time spent fixing problems than actually running.
- Inefficient energy use – Some processors overspend on oversized loaders, while others struggle with underpowered models.
- Confusing setups – Some manufacturers push overcomplicated loaders that require constant maintenance and adjustments.
The right loader should just work—delivering material smoothly, efficiently, and with minimal maintenance.
With that in mind, let’s explore what makes a great self-contained loader and how to choose the right one for your needs.
2. How Self-Contained Loaders Work in Plastics Processing
Now that we’ve defined self-contained loaders, let’s break down how they fit into a plastics processing plant.
How Material Moves in a Plant
Most plastics processors use vacuum conveying to move resin, regrind, or powders from bulk storage (like silos, bins, or gaylords) to their processing machines.
This is done using:
- A vacuum source – In this case, a self-contained loader with its own motor.
- Conveying lines – Piping or tubing that transports the material-air mixture.
- Material sources – Bulk storage containers, drying hoppers, or blenders.
- Material destinations – Injection molding machines, extruders, or other processing equipment.
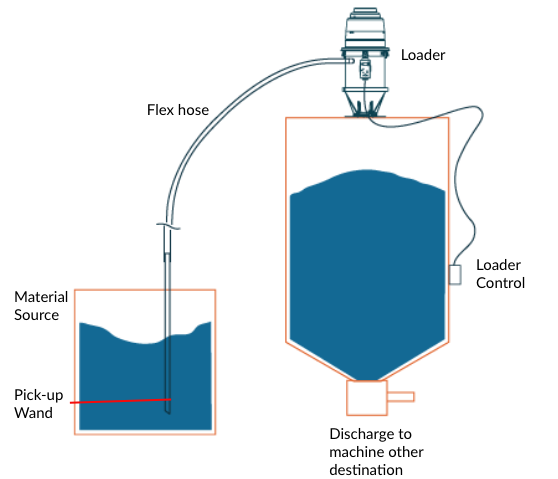
Why Choose a Self-Contained Loader?
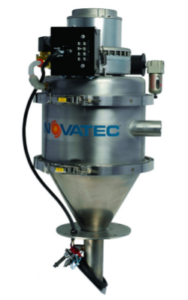
- Easy to Install & Use – No central vacuum pump or complex plumbing required.
- Perfect for Small-to-Mid-Size Operations – Best for processors running under 6 machines with material transferred over short distances.
- Independent Material Supply – No reliance on a centralized system.
If your facility is growing rapidly, you may eventually need to consider a central vacuum system—but for now, self-contained loaders are the simplest and most cost-effective solution.
But not all loaders are built the same—and choosing the right one can make or break your operation.
3. Key Features & Components of a Self-Contained Loader
Not all self-contained loaders perform equally—and the wrong choice can lead to unnecessary downtime, inefficiency, and costly maintenance.
To make an informed decision, you need to know what separates a great loader from a mediocre one.
Every self-contained loader has several key components, each of which affects performance, maintenance, and longevity.
1. The Vacuum Motor – Brushed vs. Brushless
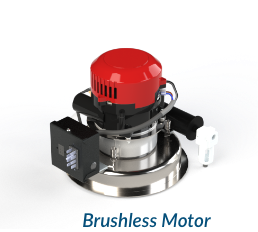
- Brushed Motors – Lower upfront cost but require periodic brush replacements
- Brushless Motors – No brushes to replace, meaning less maintenance and fewer service interruptions. Ideal for processors who want set-it-and-forget-it reliability.
Why This Matters: Some manufacturers only offer one type of motor—which means you might be forced into an option that doesn’t fit your operation.
At Novatec we offer both brushed and brushless loaders, so you get the right fit for your needs, whether you prioritize lower upfront cost or long-term maintenance reduction.
2. Filters – Standard vs. Powder-Specific
The filter keeps dust and fines from entering the vacuum motor—but not all filters are built the same.
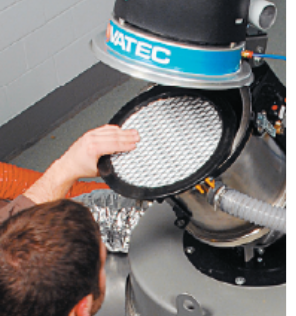
- Standard Filters – Work well for pellets and most regrind.
- Powder-Specific Filters – Needed for PVC, calcium carbonate, and other dusty materials, including some finely ground regrind.
Why Some Loaders Clog Constantly: Standard loaders aren’t designed for powders or extremely fine materials—but some manufacturers won’t tell you that upfront. If your material produces excessive fines, a powder-optimized loader can prevent clogging and extend filter life.
3. Discharge Valves – Why Some Loaders Struggle with Material Flow
Every loader releases material into the processing machine through a discharge valve. But some materials flow easily, while others tend to bridge and clog.
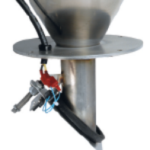
- Pellets and free-flowing materials – Standard gravity flappers work well.
- Regrind, powders, and irregular shapes – Require larger or assisted discharge valves to prevent bridging
How Novatec Solves This: Novatec’s GSL and XSL loaders use SureSeal™ metal-to-metal flappers, creating an airtight seal that prevents leaks and ensures smooth discharge. VL and VLP models feature gasketed flappers, providing effective sealing to maintain consistent material flow. These designs help keep material moving efficiently, minimizing interruptions and downtime.
4. Blowback Systems – Keeping Filters Clean
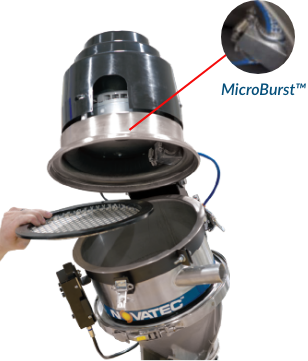
In a self-contained vacuum loader, the filter plays a critical role in trapping dust and fines before they reach the motor. But frequent loading cycles pull in not just resin, but also dust, fines, and airborne contaminants, causing filters to clog over time. A clogged filter restricts airflow, reduces conveying efficiency, and increases maintenance needs.
- Standard Blowback Systems – Use a compressed air pulse to remove dust after each loading cycle.
- MicroBurst™ Blowback (available on Novatec XSL & GSL Loaders) – Uses optimized, high-efficiency pulses to keep filters cleaner for longer while reducing compressed air usage.
Why This Matters: MicroBurst™ prevents premature clogging and minimizes downtime—meaning fewer filter cleanings and longer-lasting performance.
5. Control Systems – Simple vs. Smart
Not all loaders control material flow the same way. The right control system depends on how much automation you need.
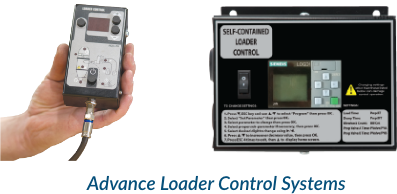
- Basic Loaders – Simple on/off operation, best for straightforward material loading.
- Advanced Loaders – Offer proportioning, timed loading, and purge functions for better process control.
Novatec’s motorized loaders feature easy-to-use digital controllers—giving you automation without overcomplicated software.
4. Powder Loaders vs. Standard Loaders: What You Need to Know
Many processors don’t realize there’s a difference between standard and powder-specific loaders—until their loader keeps clogging
Standard Loaders → Designed for Pellets & Regrind
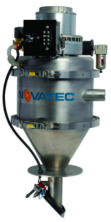
- Work well for pelletized or regrind materials.
- Standard polyester felt filters capture fines from pelletized or regrind materials but require more frequent cleaning when handling brittle or excessively dusty resins.
- Not ideal for materials that generate excessive fines, dust, or powders
Powder Loaders → Built for Challenging Materials
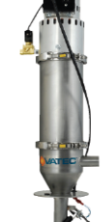
- Larger filter surface area allows for better airflow and reduced clogging.
- PTFE-coated filters minimize material buildup and make cleaning easier.
- Automatic blowback cleaning clears dust buildup and extends the time between filter maintenance—helping prevent fines from clogging filters, escaping into the motor, or causing blower wear.
Why This Matters: While some processors try using standard loaders for powders, the filters clog faster, reducing efficiency and increasing downtime—and in some cases, fines can bypass the filter entirely, leading to motor damage or failure.
Novatec’s VLP Series is specifically engineered for powders and fine materials, using expanded filter surface area, finer filtration, and optimized air pulses to prevent clogging—so you spend less time on maintenance and more time running production.
5. Compressed Air Loaders: Where They Work & Where They Don't
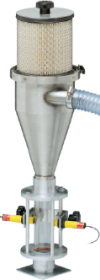
Many processors assume compressed air loaders are a cheaper option—until they see the air costs add up.
What They Are: Instead of an electric vacuum motor, compressed air loaders use a venturi system to generate suction, requiring minimal electricity for control functions.
When They Work Well
- For small-scale additive feeding in blending operations.
- When no dedicated electrical outlet is available and compressed air is readily accessible.
- For evacuating a granulator into a collection drum where material loads are small and infrequent.
When They Don’t Work Well
- High air consumption makes them costly for anything beyond light-duty use.
- Not ideal for high-throughput operations due to airflow and distance limitations.
- Can strain plant-wide air supply, affecting other equipment that depends on compressed air.
Why This Matters: Compressed air is not free—it requires significant energy to generate, and using too much can reduce efficiency in other areas of the plant.
Novatec’s AL Series is a great option for niche, small-scale applications, but most processors find that a standard vacuum loader is the better long-term investment as their operation grows.
6. The Full Breakdown: Types of Loaders (And When to Use Each One)
Now that we’ve covered how loaders work, key features, and common challenges, let’s break down the different types of self-contained loaders—so you can find the best fit for your operation.
Some manufacturers only offer a few types of loaders, expecting them to work for every application—but at Novatec, we know different operations require different solutions.
Here’s how our loader lineup compares, so you can choose the right tool for the job.
1. VL Series – The Industry’s Workhorse
Best for general-purpose pellet & regrind conveying.
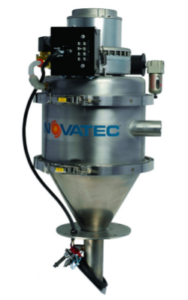
- Brushed motor – Reliable but requires regular brush replacements. (Optional brushless upgrade available)
- External blowback accumulator – Helps keep filters clean after each cycle.
- Modular body design with 1.5” and 2” line size options – Fits standard setups.
- Simple PLC-based control – Easy-to-use system with straightforward operation.
- Tried-and-true reliability – A standard in plastics plants.
Where It Falls Short: VL loaders require brush replacements and gasket maintenance, leading to more frequent downtime over time.
Perfect for: Processors who need a basic, cost-effective solution and don’t mind routine maintenance.
For more details, visit the VL Series product page.
2. GSL Series – The Premium Ultra-Low Maintenance Option
Best for high-throughput processors who want maximum uptime and the lowest cost of ownership.
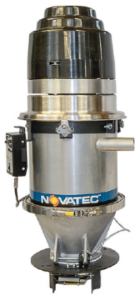
- Brushless motor – No brushes to replace, eliminating routine motor maintenance.
- MicroBurst™ Internal Blowback – Keeps filters cleaner for longer, reducing downtime.
- SureSeal™ Metal-to-Metal Flapper – No gaskets to wear out or replace.
- 3-inch discharge – Larger opening for improved flow, reducing material bridging.
- Tilt Cleanout & Hinged Lid – Easiest maintenance access in the industry.
- Up to twice the throughput of the equivalent volume VL (up to 1000 lb/hr).
How GSL Reduces Maintenance & Downtime: Unlike VL and XSL models, GSL eliminates the most common maintenance tasks—motor brush replacements and gasket wear—while significantly reducing filter cleanings. This means fewer stoppages, reduced labor costs, and higher operational efficiency. While routine checks are still required, GSL delivers the lowest maintenance demands of any loader in its class.
Perfect for: Processors who prioritize uptime, efficiency, and drastically reduced maintenance.
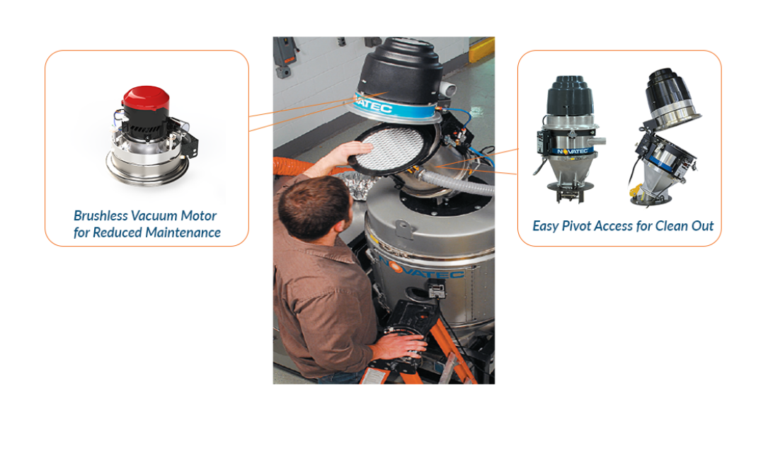
For a closer look, visit the GSL Series product page.
3. XSL Series – A Step Up, But Not Maintenance-Free
Best for processors who want premium features but can tolerate some maintenance
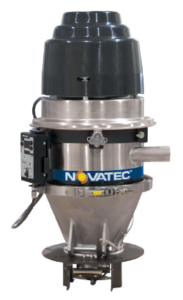
- Brushed motor – Improved performance over VL, but still requires brush replacements.
- Includes premium GSL features – MicroBurst™ blowback, SureSeal™ flapper, Tilt Cleanout, Hinged Lid, and 3-inch discharge for improved material flow.
- More cost-effective than GSL while offering some premium performance features.
Key Consideration: XSL offers a strong upgrade from VL, incorporating premium features for better efficiency. However, since it still uses a brushed motor, routine brush replacements are necessary over time. Processors looking to reduce maintenance as much as possible may prefer the GSL Series, which eliminates brush changes and gasket wear entirely.
Perfect for: Processors who want GSL’s efficiency at a lower upfront cost but are willing to deal with periodic motor maintenance.
Explore further on the XSL Series product page.
4. VLP Series – The Powder & Dusty Regrind Specialist
Best for powders, PVC, and dusty materials
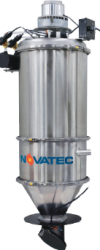
- Expanded filter surface – Designed for finer filtration.
- PTFE-coated filters – Prevents clogging and increases ease of cleaning.
- Automatic blowback filter cleaning – Extends filter life and reduces maintenance.
Why Standard Loaders Can’t Handle Powders: Many processors try using standard loaders for powders but experience frequent clogs, rapid filter degradation, and excess fines bypassing into the motor—leading to performance issues over time. The VLP Series is built specifically for powders, ensuring longer filter life and fewer shutdowns for cleaning.
Perfect for: Processors running PVC, calcium carbonate, and other dusty materials that cause clogging in standard loaders.
More information is available on the VLP Series product page.
5. AL Series – The Compressed Air Loader (Niche Use Case)
Best for processors who need an air-powered loader

- No motor – Uses compressed air as the primary power source, with electricity only for demand controls.
- Best for small-scale applications where material volumes are low.
- Not ideal for high-throughput applications due to high air consumption.
Key Consideration: Compressed air loaders seem like a low-cost option upfront, but they consume significant compressed air, which can become a major expense over time. Many processors outgrow them quickly and switch to vacuum loaders for better efficiency.
Perfect for: Small-scale applications and additive feeding, but most processors will get better long-term value from a vacuum loader.
For specifics, visit the AL Series product page.
6. GVL Series – The Blender-Specific Loader
Best for feeding blenders & precise material layering
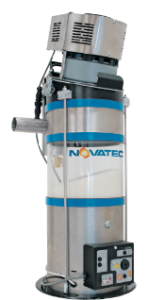
- Clear GlassVu™ chamber – Full visibility of material loading.
- Positive-sealing pneumatic discharge valve – No bridging, no material loss.
- Infrared sensor below the slide gate – Ensures precise demand loading.
Why This Loader Stands Out: Blenders require precise layering and material visibility. The GVL Series ensures accurate material flow and real-time monitoring, making it an essential tool for processors relying on blending accuracy.
Perfect for: Processors using blenders that require controlled, precise material loading with full visibility.
Find out more on the GVL Series product page.
Final Thoughts: Finding the Right Fit for Your Operation
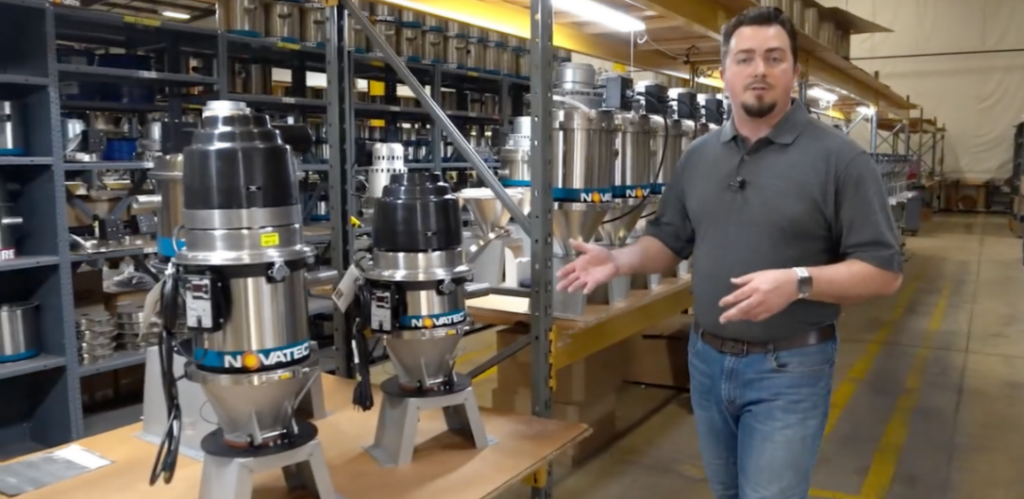
Every operation has unique material handling needs, and the right loader depends on factors like throughput, maintenance priorities, and long-term cost considerations.
For processors who need a low-cost, straightforward solution, the VL Series offers proven reliability, while the XSL Series adds key performance upgrades for those willing to handle some maintenance. For operations that prioritize uptime, reduced labor costs, and long-term efficiency, many processors find that the GSL Series provides the lowest-maintenance, most cost-effective solution over time.
Novatec’s full lineup ensures there’s an option for every type of operation. Whether you need a loader for powders, additives, or high-throughput production, selecting a model that minimizes downtime and maintenance can have a significant impact on overall efficiency and operating costs.
Still weighing your options? Swing by Novatec’s Loaders page—or drop us a line using the form below.
No pressure. No sales pitch. Just a conversation about what makes the most sense for your plant.
Because the right loader isn’t just another piece of equipment—it’s the key to keeping production flowing, minimizing maintenance, and making your operation more efficient.
Let’s find the right fit together!
Submit A Question: Conveying
Ask the Expert
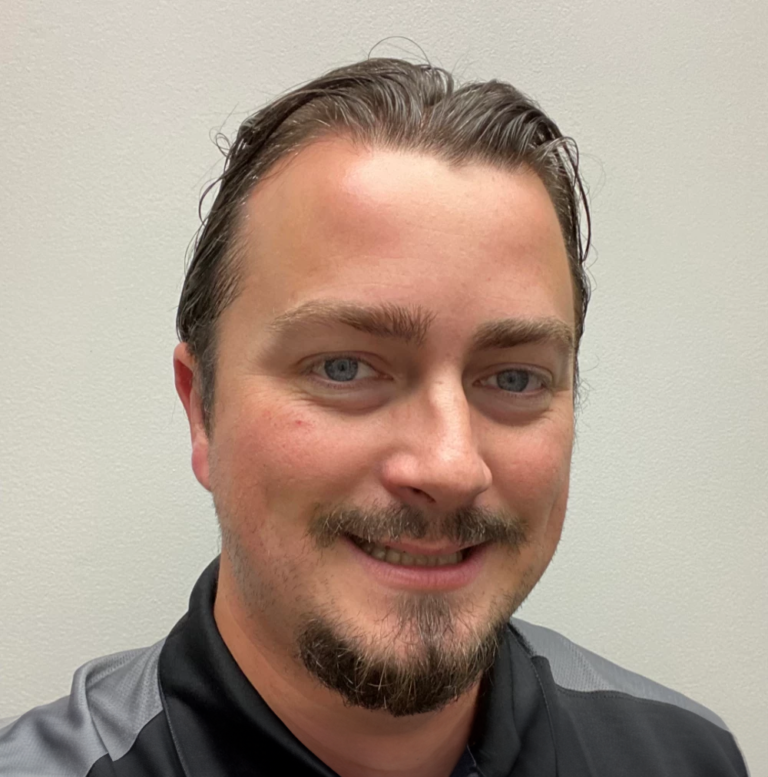